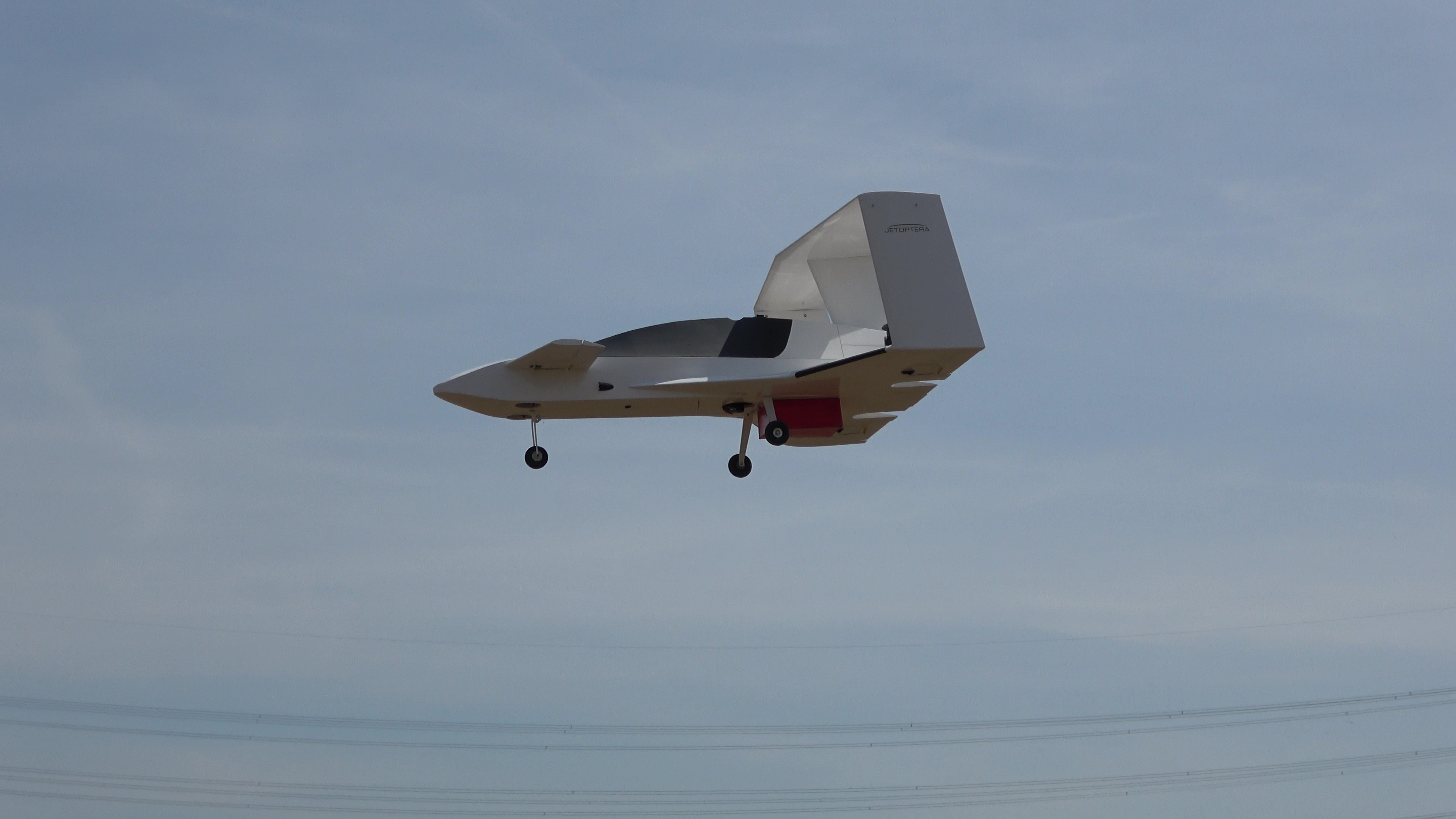
Jetoptera, a start-up developing innovative VTOL and STOL aircraft concepts using bladeless fan technology, has completed its fourth small business innovation and research (SBIR) contract for the U.S. Air Force as part of the development work for a High Speed VTOL (HSVTOL) military aircraft. The Washington-based company this week reported that it has conducted an initial evaluation of what it calls its “3-in-1” propulsion system and is preparing to start wind-tunnel tests with a subscale model.
The Jetoptera HSVTOL concept is based on its patented fluidic propulsion system (FPS). The company says the technology is scalable and can power aircraft with a takeoff weight of up to 10,000 pounds (4,500 kilograms).
For the latest SBIR contract, Jetoptera designed, built, and tested an upper-surface blown wing structure fitted with what it referred to as “a powered-high-lift test article” that incorporates the FPS. The company plans to use the data from these tests to optimize the conceptual design for an HSVTOL aircraft it has said could be ready to fly in 2025.
In a January 11 statement, Jetoptera said that it expects the conceptual aircraft to fly at speeds of around Mach 0.8, which it says will be twice as fast as a tiltrotor aircraft can travel. Under a separate STTR Phase II contract for the Air Force, it intends to validate the design during the first half of 2023.
The work for the Air Force was conducted with Northrop Grumman subsidiary Scaled Composites, which helped with the design of the high lift system and test article. Static testing was performed with Scaled Composites using an off-the-shelf electric booster compressor procured for the program.
Breakthroughs Include Greater Lift
According to Jetoptera, the partners achieved several technical breakthroughs, including testing with an electric air compressor feeding the FPS thruster-ejectors, which are used to distribute primary air for hybrid or all-electric systems. It also demonstrated lift co-efficients of greater than 8.0, which the company said is up to 40 percent better than propeller-blown wing units demonstrated by other programs, as well as recording lower noise and vibrations.
Like Dyson’s bladeless electric fans for domestic equipment such as vacuum cleaners, the FPS has no visible moving parts or propellers. Rather, the technology uses a relatively small flow of compressed air from a turbo-compressor to suck in a much greater volume of ambient air, creating a vortex that significantly amplifies the airflow through an aerodynamic loop. Additional thrusters augment the thrust output of the FPS.